Gas sensor: Difference between revisions
Line 155: | Line 155: | ||
'''Hardware Connections''' | '''Hardware Connections''' | ||
[[File:Arduino Uno.jpeg|300px|thumb|Left|Connections on the Arduino Uno | [[File:Arduino Uno.jpeg|300px|thumb|Left|Connections on the Arduino Uno microcontroller]] | ||
We followed the design schematics to make connections between the gas sensors and an Arduino microcontroller. This included correctly attaching the sensor’s data output pins to the appropriate input ports on the microcontroller and ensuring proper power and ground connections. The accuracy of these connections is crucial for the success of the experiment, so we carefully checked all connection points to ensure they were correct. The final connection situation is shown in Figure 3.2。 | We followed the design schematics to make connections between the gas sensors and an Arduino microcontroller. This included correctly attaching the sensor’s data output pins to the appropriate input ports on the microcontroller and ensuring proper power and ground connections. The accuracy of these connections is crucial for the success of the experiment, so we carefully checked all connection points to ensure they were correct. The final connection situation is shown in Figure 3.2。 | ||
'''Software Configuration''' | |||
Once the hardware connections were completed, we connected the Arduino microcontroller to a computer via a USB interface. On the computer, we launched the Arduino IDE software and loaded code specifically designed for testing CO2 concentrations. This software environment allowed us to upload code to the microcontroller and monitor the running program and data output from the sensors. | |||
[[File:Arduino Interface.jpeg|300px|thumb|Left|Interfaces on the Arduino IDE software]] | |||
'''Communication Parameter Adjustment''' | |||
After initially running the test code, we discovered that minor adjustments to the communication addresses were necessary to ensure stable and reliable data transfer between the microcontroller and the gas sensors. After adjusting these parameters, we approached the sensor and exhaled near it to test its responsiveness to changes in CO2 concentration. This helped us evaluate the sensor's reaction speed and accuracy to environmental changes. | |||
'''System Testing and Setup''' | |||
After confirming that the hardware connections were correct and the software could control the sensor accurately, we conducted a series of functional tests on the sensors. For example, we hold the sensor and exhale it from far to near. The results indicated that all hardware and software were functioning properly, and the sensors' sensitivity and response characteristics met the experimental requirements. Subsequently, we began constructing the final experimental setup, preparing to enter the data collection phase. |
Revision as of 23:55, 26 April 2024
Introduction
The semiconductor gas sensor for carbon monoxide/combustible gas detection uses a gas-sensitive material, tin dioxide (SnO2), which has a low conductivity in clean air. The high and low-temperature cycle detection method is used to detect carbon monoxide at low temperature (1.5V heating), where the conductivity of the sensor increases with the concentration of carbon monoxide gas in the air, and to detect the combustible gases methane and propane at high temperature (5.0V heating), and to clean up the stray gases that are adsorbed at low temperature. A simple circuit is used to convert the change in conductivity to an output signal corresponding to the concentration of the gas.
Team Members
Fu Xinming, Ge Yexiao, Yang Haoqing
Setup
The diagram above shows the basic test circuit for the sensor. The sensor requires two voltages to be applied: the heater voltage (VH) and the test voltage (VC). VH is used to provide the sensor with a specific operating temperature and VC is used to determine the voltage (VRL) across the load resistor (RL) connected in series with the sensor. VC is used to determine the voltage (VRL) across the load resistor (RL) in series with the sensor. The sensor has a slight VC requires a DC power supply. VC and VH can be used as long as the electrical requirements of the sensor are met. VC and VH can share the same power supply circuit if the electrical requirements of the sensor are met. To take advantage of the sensor's performance of the sensor, it is necessary to select the appropriate RL value.
Equipment
Gas Sensitive Components
One-chip computer/microcontroller
ADC conversion module
Datasheets
Gas Sensor ENS160_Datasheet
Temperature Sensor Temperature sensor
Timeline and Milestone
Week 8 (3/4 — 3/8) | Debug sensor module hardware devices and software code | |
Week 9 — Week 10(3/11 — 3/22) | Measurements using gas sensors to obtain a database | |
Week 11 — Week 12(3/25 — 4/5) | Fit curve to obtain the corresponding relationship between the output value and the gas concentration | |
Week 13 (4/8 — 4/12) | Analyze experimental results and complete reports |
Expected Results
We hope to obtain a curve between the output value and the corresponding gas concentration, so as to know the pollution situation in the environment relatively accurately.
Report
Introduction
Band Theory
Band theory explains that within a crystal lattice, there exists a valence band and a conduction band separated by an energy gap, which is closely related to the Fermi level. The Fermi level is defined as the highest energy level occupied by electrons at absolute zero temperature. Based on the size of the energy gap between these bands, materials are classified into three main categories:
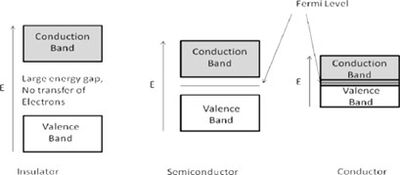
Insulators: These materials have a substantial gap between the valence and conduction bands, typically around 10 eV or more. Due to this large gap, a significant amount of energy is needed to move an electron into the conduction band, resulting in negligible electronic conduction. At zero temperature, the Fermi level represents the highest filled state.
Semiconductors: These materials feature an energy gap ranging from about 0.5 to 5.0 eV. Below the Fermi level, electrons do not have enough energy to bridge this gap, preventing conduction. However, once the energy exceeds the Fermi level, electrons can transition to the conduction band, leading to increased electrical conductivity.
Conductors: In conductors, the Fermi level is positioned within the conduction band itself, allowing for continuous electron flow and high conductivity.
Band Theory in Gas Sensors
Band theory has played a crucial role in understanding the functionality of gas sensors for several years. In this context, the interaction between a target gas and a metal oxide film's surface—typically involving surface adsorbed oxygen ions—causes a shift in the material's charge carrier concentration. This shift subsequently affects the material's conductivity or resistivity.
For n-type materials, oxidizing gases increase the resistance of the thin film, while reducing gases decrease it. The opposite is true for p-type materials. This interaction, involving oxidation-reduction (REDOX) reactions, alongside the transduction function, defines the chemiresistive behavior of these sensors. Metal oxide sensors are commonly configured as sintered pellets or as thick and thin films. The specific geometry of the crystallites and their interconnections significantly influence these receptor and transduction functions, highlighting the impact of nanotechnology in enhancing sensor performance by manipulating materials at the atomic and molecular scale.
On the other hand, p-type semiconductors, where positive holes are the majority charge carriers, exhibit increased conductivity in the presence of an oxidizing gas, which augments the number of positive holes. Conversely, the presence of a reducing gas increases the material's resistance by introducing negative charge that diminishes the concentration of positive charge carriers (holes). The various responses of these materials to different gases are summarized in Table 1.
Classification | Oxidising Gases | Reducing Gases |
---|---|---|
n-type | Resistance increase | Resistance decrease |
p-type | Resistance decrease | Resistance increase |
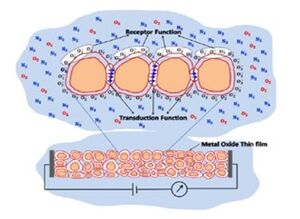
The chemiresistance of metal oxides is also linked to the width of the space charge region that forms on the crystallites due to electron transfer during the adsorption and desorption of gas molecules. This space charge region creates a potential barrier that affects conduction between the grains, leading to changes in the Fermi level. In n-type materials, the interaction with oxidizing gases causes the energy bands to bend upward as electrons are depleted, whereas with reducing gases, the bands bend downward due to electron accumulation. Thus, the space charge region and band bending are closely related to the carrier concentrations within the grain, which are influenced by the grain's size and shape.
Why carbon dioxide?
As of March 2024, carbon dioxide concentrations in the Earth's atmosphere were recorded at 425 ppm. Carbon dioxide is utilized in a variety of ways including in carbonated beverages, pneumatic systems, fire extinguishers, and as a critical component for photosynthesis. Additionally, it is used in lasers and refrigeration systems, both naturally and in human applications.
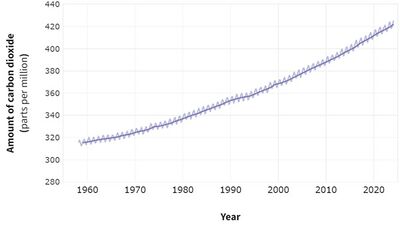
Carbon dioxide also acts as a greenhouse gas, absorbing infrared energy from the atmosphere. This absorption causes the gas to vibrate, subsequently transferring heat to the surrounding air and raising the ambient temperature. Increased levels of carbon dioxide can lead to higher temperatures. Therefore, accurate and reliable sensors that can operate within appropriate temperature ranges are crucial for monitoring changes in atmospheric carbon dioxide concentrations. The recent rise in carbon dioxide levels, primarily due to human activities such as the combustion of hydrocarbons and other carbon-containing fuels like coal, methane, petrol, and kerosene, has heightened concerns about its contribution to global warming. Such activities, when combined with oxygen, produce carbon dioxide and water. Monitoring the emissions of CO2 during these combustion processes is vital as it provides essential real-time data on the quantity of carbon dioxide being emitted.
CO2 Concentration and Exposure time | Effect on Health (symptoms) |
---|---|
0.035% | Approximate atmospheric concentration, no noticeable effect. |
3.3–5.4% for 15 mins | Increased depth of breathing |
7.5% for 15 mins | Feeling of an inability to breathe, increased pulse rate, headache, dizziness, sweating, restlessness, disorientation, and visual distortion. |
3%, for over 15 hours | Decreased night vision, colour sensitivity |
10%, 1.5 mins | Eye flickering, increased muscle activity, twitching |
10+% | Difficulty in breathing, impaired hearing, nausea, vomiting, a strangling sensation, sweating, after 15 minutes a loss of consciousness. |
30% | Unconsciousness, convulsions. Several deaths attributed to CO2 at concentrations of more than 20% |
Since 1958, atmospheric carbon dioxide levels have consistently increased and are expected to continue rising as long as there is a demand for fossil fuel combustion. High concentrations of carbon dioxide can have significant adverse health effects, including drowsiness and, at very high levels, suffocation.
The National Environmental Agency (NEA) recommends indoor CO2 levels that should ideally not exceed 800 ppm. Thus, the ability to measure and control carbon dioxide levels is crucial for maintaining indoor air quality and protecting human health.
Experimental Procedure
Temperature Sensor test
Background
In this experiment, it is essential to ensure that the TVOC and CO2 gas sensors operate accurately under various environmental temperature and humidity conditions. Since the performance of these sensors—such as range, sensitivity, and accuracy—can be significantly affected by ambient temperature and humidity, the introduction of a temperature sensor for simultaneous measurement becomes crucial. This setup allows for real-time monitoring of the experimental environment’s temperature, thus enabling the calibration of the gas sensors' readings for more accurate data.
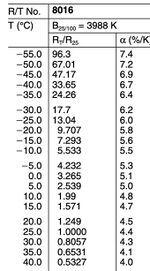
Principle of the Temperature Sensor
We chose the NTC thermistor, whose model No. is B57861S0103F040, as our temperature sensor. The resistance of an NTC thermistor decreases as the temperature increases. This characteristic is due to the properties of its semiconductor material, where more charge carriers (electrons and holes) participate in conduction at higher temperatures, reducing resistance. Additionally, the NTC thermistor used in the experiment has a specific B value, an important parameter describing its temperature sensitivity. The B value, determined between two specific temperatures (usually 25°C and 100°C), characterizes the rate at which the resistance changes with temperature. With a B value of 3988K and a nominal resistance of 10kΩ at 25°C, this sensor demonstrates sensitivity to changes within a specific temperature range.
Test Process
Prior to the experiments, under the help of professor, we attached the NTC thermistor to a cable using soldering techniques, being mindful to control the soldering temperature and duration to prevent overheating damage. After soldering, we measured the sensor’s resistance with a multimeter and converted these readings to temperatures using the resistance-temperature (R/T) characteristic curve from the datasheet as shown
Experimental Verification
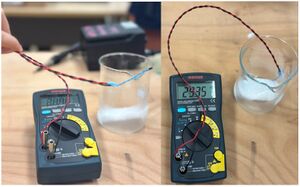
As illustrated in the experimental design diagram, we tested the temperature sensor in a beaker containing dry ice. The sublimation of dry ice absorbs heat from its surroundings, reducing the temperature inside the beaker, thereby providing a dynamic environment to test the sensor's responsiveness and accuracy. Preliminary measurements indicated a significant drop in ambient temperature, approximately 5°C, demonstrating the sensor's capability to accurately respond to low-temperature changes.
Gas Sensor Calibration
After verifying the performance and reliability of the temperature sensor, we proceeded to calibrate another key component in the experiment—the gas sensors. The primary goal here was to ensure proper interfacing and communication between the gas sensors and a microcontroller, thus providing a reliable hardware foundation for accurate CO2 concentration measurement.
Hardware Connections
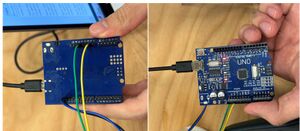
We followed the design schematics to make connections between the gas sensors and an Arduino microcontroller. This included correctly attaching the sensor’s data output pins to the appropriate input ports on the microcontroller and ensuring proper power and ground connections. The accuracy of these connections is crucial for the success of the experiment, so we carefully checked all connection points to ensure they were correct. The final connection situation is shown in Figure 3.2。
Software Configuration
Once the hardware connections were completed, we connected the Arduino microcontroller to a computer via a USB interface. On the computer, we launched the Arduino IDE software and loaded code specifically designed for testing CO2 concentrations. This software environment allowed us to upload code to the microcontroller and monitor the running program and data output from the sensors.
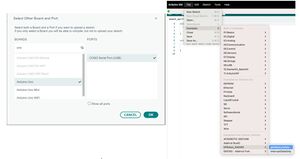
Communication Parameter Adjustment
After initially running the test code, we discovered that minor adjustments to the communication addresses were necessary to ensure stable and reliable data transfer between the microcontroller and the gas sensors. After adjusting these parameters, we approached the sensor and exhaled near it to test its responsiveness to changes in CO2 concentration. This helped us evaluate the sensor's reaction speed and accuracy to environmental changes.
System Testing and Setup
After confirming that the hardware connections were correct and the software could control the sensor accurately, we conducted a series of functional tests on the sensors. For example, we hold the sensor and exhale it from far to near. The results indicated that all hardware and software were functioning properly, and the sensors' sensitivity and response characteristics met the experimental requirements. Subsequently, we began constructing the final experimental setup, preparing to enter the data collection phase.